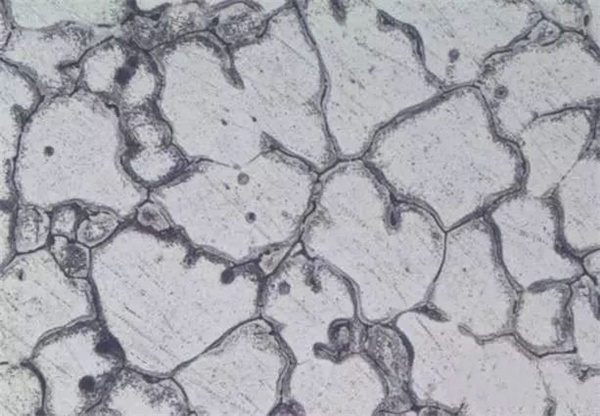
I. කෙටි කිරීම
සමහර නිස්සාරණය කරන ලද නිෂ්පාදනවල වලිගය අවසානයේ, අඩු විශාලන පරීක්ෂාවකින් පසු, හරස්කඩයේ මැද කොටසෙහි අං වැනි සංසිද්ධියක් ඇති අතර එය හැකිලීමේ වලිගය ලෙස හැඳින්වේ.
සාමාන්යයෙන්, ඉදිරි නිස්සාරණ නිෂ්පාදනයේ වලිගය ප්රතිලෝම නිස්සාරණයට වඩා දිගු වන අතර මෘදු මිශ්ර ලෝහය දෘඩ මිශ්ර ලෝහයට වඩා දිගු වේ.ඉදිරියට නෙරා ඇති නිෂ්පාදනයේ හැකිලීම බොහෝ දුරට වළයාකාර විසංයෝජන ස්ථරයක ස්වරූපයෙන් වන අතර ප්රතිලෝම නිස්සාරණය කරන ලද නිෂ්පාදනයේ හැකිලීම බොහෝ දුරට මධ්යම පුනීලයක හැඩයෙන් යුක්ත වේ.
ලෝහය පිටුපස කෙළවරට නෙරා ඇති අතර, නිස්සාරණ සිලින්ඩරයේ හෝ ගෑස්කට් එකේ මළ කෙළවරේ එකතු වී ඇති ඉන්ගෝට් සම සහ විදේශීය ඇතුළත් කිරීම් ද්විතියික හැකිලීමක් සෑදීම සඳහා නිෂ්පාදනයට ගලා යයි;අවශේෂ ද්රව්ය ඉතා කෙටි වන විට සහ නිෂ්පාදනයේ මධ්ය ප්රමාණවත් ලෙස පෝෂණය නොකළ විට, එය සංක්ෂිප්ත වර්ගයකි.වලිගය අවසානයේ සිට ඉදිරිපස දක්වා, වලිගය ක්රමයෙන් සැහැල්ලු වන අතර සම්පූර්ණයෙන්ම අතුරුදහන් වේ.
හැකිලීමේ ප්රධාන හේතුව
1. අවශේෂ ද්රව්ය ඉතා කෙටි හෝ නිෂ්පාදනයේ කැපුම් කෙළවරේ දිග රෙගුලාසිවලට අනුකූල නොවේ;
2. extrusion pad පිරිසිදු නොවන අතර තෙල් පැල්ලම් ඇත;
3. නිස්සාරණයේ පසු අවධියේදී, නිස්සාරණ වේගය ඉතා වේගවත් හෝ හදිසියේ වැඩි වේ;
4. විකෘති වූ මිරිකා පෑඩ් භාවිතා කරන්න (මැදෙහි උස් වූ පෑඩ්);
5. නිස්සාරණ සිලින්ඩරයේ උෂ්ණත්වය ඉතා ඉහළ ය;
6. extrusion සිලින්ඩරය සහ extrusion shaft එක පෙළගස්වා නැත;
7. ඉන්ගෝට් මතුපිට පිරිසිදු නැත, තෙල් පැල්ලම් ඇත, වෙන් කිරීමේ පිළිකා සහ නැමීම් සහ අනෙකුත් දෝෂ ඉවත් නොකෙරේ;
8. නිස්සාරණ සිලින්ඩරයේ අභ්යන්තර කමිසය පිරිසිදු හෝ විකෘති වී නොමැති අතර ඇතුළත ලයිනිං නියමිත වේලාවට පිරිසිදු කිරීමේ පෑඩ් එකකින් පිරිසිදු නොවේ.
වැළැක්වීමේ ක්රමය
1. අවශේෂ ඉතිරි කර අවශ්ය පරිදි වලිග කපා දමන්න;
2. අච්චු පිරිසිදුව තබා ගන්න;
3. ඉන්ගෝට් මතුපිට ගුණාත්මකභාවය වැඩි දියුණු කිරීම;
4. සුමට නිස්සාරණය සහතික කිරීම සඳහා නිස්සාරණ උෂ්ණත්වය සහ වේගය සාධාරණ ලෙස පාලනය කරන්න;
5. විශේෂ අවස්ථා හැර, මෙවලම සහ අච්චුවේ මතුපිට තෙල් යෙදීම දැඩි ලෙස තහනම්ය;
6. ගෑස්කට් නිසි ලෙස සිසිල් කර ඇත.
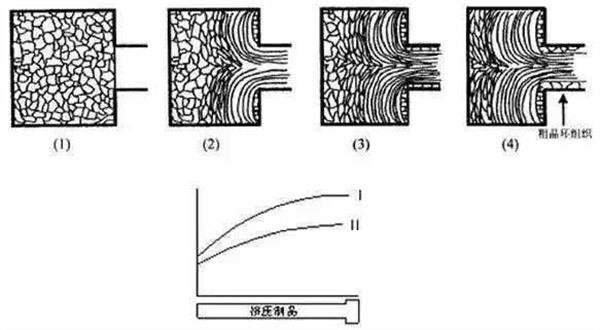
II.රළු ස්ඵටික වළල්ල
සමහර ඇලුමිනියම් මිශ්ර ලෝහ නිස්සාරණය කරන ලද නිෂ්පාදන ද්රාවණ ප්රතිකාරයෙන් පසු අඩු විශාලන පරීක්ෂණ කැබැල්ල මත නිෂ්පාදනයේ පරිධිය දිගේ රළු ප්රතිස්ඵටිකීකරණය කරන ලද ධාන්ය ව්යුහ ප්රදේශයක් සාදයි, එය රළු ධාන්ය වළල්ලක් ලෙස හැඳින්වේ.නිෂ්පාදනවල විවිධ හැඩයන් සහ සැකසුම් ක්රම හේතුවෙන්, මුදු හැඩැති, චාප හැඩැති සහ වෙනත් ආකාරයේ රළු මුදු සෑදිය හැකිය.ගොරෝසු වළල්ලේ ගැඹුර වලිගයේ සිට ඉදිරිපස දක්වා ක්රමයෙන් අඩු වී සම්පූර්ණයෙන්ම අතුරුදහන් වේ.ප්රාථමික සෑදීමේ යාන්ත්රණය උණුසුම් නිස්සාරණයෙන් පසු නිෂ්පාදනයේ මතුපිට ඇති උප-ධාන්ය කලාපය වන අතර රළු ප්රතිස්ඵටිකීකරණය කරන ලද ධාන්ය කලාපය රත් කිරීමෙන් සහ ද්රාවණ ප්රතිකාරයෙන් පසුව සෑදී ඇත.
රළු ස්ඵටික වළල්ලේ ප්රධාන හේතුව
1. අසමාන නිස්සාරණ විරූපණය
2. තාප පිරියම් කිරීමේ උෂ්ණත්වය ඉතා ඉහළ වන අතර රඳවා තබා ගැනීමේ කාලය ඉතා දිගු වේ, එම නිසා ධාන්ය වර්ධනය වේ;
3. රත්රන්වල රසායනික සංයුතිය අසාධාරණ ය;
4. සාමාන්ය තාප පිරියම් කළ හැකි ශක්තිමත් කිරීමේ මිශ්ර ලෝහ තාප පිරියම් කිරීමෙන් පසු රළු මුදු ඇත, විශේෂයෙන් 6a02, 2a50 සහ අනෙකුත් මිශ්ර ලෝහවල හැඩතල සහ බාර් වඩාත් බරපතල වන අතර ඒවා ඉවත් කළ නොහැකි අතර එය යම් පරාසයක් තුළ පමණක් පාලනය කළ හැකිය;
5. පිටකිරීමේ විරූපණය කුඩා හෝ විරූපණය ප්රමාණවත් නොවේ, හෝ විවේචනාත්මක විරූපණ පරාසය තුළ, රළු ස්ඵටික වළල්ලක් නිෂ්පාදනය කිරීම පහසුය.
වැළැක්වීමේ ක්රමය
1. නිස්සාරණ සිලින්ඩරයේ අභ්යන්තර බිත්තිය සිනිඳු සහ පිරිසිදු වන අතර, නිස්සාරණය අතරතුර ඝර්ෂණය අඩු කිරීම සඳහා සම්පූර්ණ ඇලුමිනියම් කමිසයක් සාදයි;
2. විරූපණය හැකි තරම් සම්පූර්ණ හා ඒකාකාරී විය යුතු අතර, උෂ්ණත්වය සහ වේගය වැනි ක්රියාවලි පරාමිතීන් සාධාරණ ලෙස පාලනය කළ යුතුය;
3. විසඳුම ප්රතිකාර උෂ්ණත්වය ඉතා ඉහළ හෝ රඳවා තබා ගැනීමේ කාලය ඉතා දිගු වීම වැළැක්වීම;
4. porous die සමඟ නිස්සාරණය;
5. ප්රතිලෝම නිස්සාරණ ක්රමය සහ ස්ථිතික නිස්සාරණ ක්රමය මගින් නිස්සාරණය;
6. ද්රාවණ ප්රතිකාර-ඇඳීමේ-වයස්ගත ක්රමය මගින් නිෂ්පාදනය කරනු ලැබේ;
7. සම්පූර්ණ රන් සංයුතිය සකස් කර නැවත ස්ඵටිකීකරණ නිෂේධන මූලද්රව්යය වැඩි කරන්න;
8. ඉහළ උෂ්ණත්ව නිස්සාරණය භාවිතා කරන්න;
9. සමහර මිශ්ර ලෝහ ඉන්ගෝට් සමජාතීය නොවන අතර, නිස්සාරණයේදී රළු ධාන්ය වළල්ල නොගැඹුරු වේ.
III, ස්ථර
මෙය ලෝහ ප්රවාහය සාපේක්ෂ වශයෙන් ඒකාකාරී වන විට සාදන ලද සමේ ඩිලමිනේෂන් දෝෂයක් වන අතර, අච්චුව සහ ඉදිරිපස ප්රත්යාස්ථ කලාපය අතර අතුරු මුහුණත දිගේ නිෂ්පාදිතය තුළට ඉන්ගෝට් මතුපිට ගලා යයි.තීර්යක් අඩු විශාලන පරීක්ෂණ කැබැල්ලේ, හරස්කඩයේ කෙළවරේ විවිධ ස්ථරවල දෝෂයක් ඇති බව පෙනේ.
ස්තරීකරණයේ ප්රධාන හේතුව
1. ඉන්ගෝට් මතුපිට දූවිලි ඇත හෝ ඉන්ගෝට් මෝටර් රථ සම, ලෝහ පිළිකා ආදිය වෙනුවට විශාල වෙන් කිරීමේ එකතුවක් ඇත, ඒවා ස්ථර සෑදීමට පහසුය;
2. නිස්සාරණයට පෙර පිරිසිදු නොකළ තෙල් පැල්ලම්, sawdust, ආදිය වැනි හිස් හෝ කුණු මතුපිට burrs ඇත;
3. ඩයි කුහරයේ පිහිටීම අසාධාරණය, නිස්සාරණ සිලින්ඩරයේ කෙළවරට සමීප වේ;
4. නිස්සාරණ මෙවලම බැරෑරුම් ලෙස පැළඳ සිටී හෝ නිස්සාරණ සිලින්ඩරයේ පඳුරෙහි අපිරිසිදුකමක් ඇති අතර එය නියමිත වේලාවට පිරිසිදු කර ප්රතිස්ථාපනය කළ නොහැක;
5. extrusion pad හි විෂ්කම්භය වෙනස ඉතා විශාලය;
6. නිස්සාරණ සිලින්ඩරයේ උෂ්ණත්වය ingot එකට වඩා බෙහෙවින් වැඩි ය.
වැළැක්වීමේ ක්රමය
1. අච්චු සාධාරණ සැලසුම් කිරීම, නියමිත වේලාවට පරීක්ෂා කිරීම සහ නුසුදුසු මෙවලම් ප්රතිස්ථාපනය කිරීම;
2. උඳුන තුල නුසුදුසු කුට්ටි ස්ථාපනය කර නැත;
3. අවශේෂ ද්රව්ය කැපීමෙන් පසු, ලිහිසි තෙල්වලට ඇලවීමකින් තොරව එය පිරිසිදු කළ යුතුය;
4. නිස්සාරණ සිලින්ඩරයේ ආස්තරය නොවෙනස්ව තබා ගන්න, නැතහොත් ගෑස්කට් එකකින් ලයිනිං නියමිත වේලාවට පිරිසිදු කරන්න.
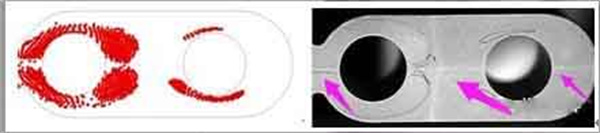
IV.දුර්වල වෙල්ඩින්
වෑල්ඩයේ ඇති බෙදීම මගින් නිස්සාරණය කරන ලද හිස් නිෂ්පාදනයේ වෑල්ඩින් ඉවත් කිරීම හෝ අසම්පූර්ණ වෑල්ඩින් කිරීමේ සංසිද්ධිය දුර්වල වෙල්ඩින් ලෙස හැඳින්වේ.
දුර්වල වෙල්ඩින් සඳහා ප්රධාන හේතුව
1. නිස්සාරණ සංගුණකය කුඩා වන අතර, නිස්සාරණ උෂ්ණත්වය අඩු වන අතර, නිස්සාරණ වේගය වේගවත් වේ;
2. නිස්සාරණ ලොම් හෝ මෙවලම් පිරිසිදු නොවේ;
3. අච්චුව තෙල්;
4. නුසුදුසු අච්චු නිර්මාණය, ප්රමාණවත් හෝ අසමතුලිත ජල ස්ථිතික පීඩනය, shunt කුහරවල අසාධාරණ නිර්මාණය;
5. ඉන්ගෝට් මතුපිට තෙල් පැල්ලමක් ඇත.
වැළැක්වීමේ ක්රමය
1. නිස්සාරණ සංගුණකය, නිස්සාරණ උෂ්ණත්වය සහ නිස්සාරණ වේගය නිසි ලෙස වැඩි කරන්න;
2. සාධාරණ සැලසුම් සහ අච්චු නිෂ්පාදනය;
3. නිස්සාරණ සිලින්ඩරය සහ නිස්සාරණ ගෑස්කට් තෙල් ආලේප කර පිරිසිදුව තබා නැත;
4. පිරිසිදු මතුපිටක් සහිත ඉන්ගෝට් භාවිතා කරන්න.
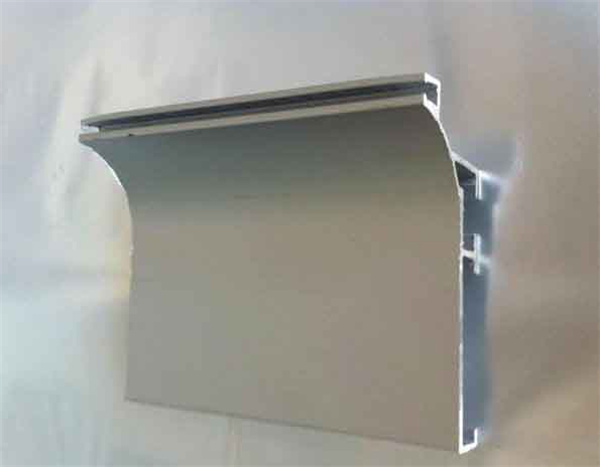
V. Extrusion ඉරිතැලීම්
මෙය නිස්සාරණය කරන ලද නිෂ්පාදනයේ තීර්යක් පරීක්ෂණ කැබැල්ලේ අද්දර කුඩා චාප හැඩැති ඉරිතැලීමක් වන අතර එහි කල්පවත්නා දිශාව දිගේ යම් කෝණයකින් වරින් වර ඉරිතැලීමක් වන අතර එය සැහැල්ලු අවස්ථා වලදී එපීඩර්මිස් යට සැඟවී ඇති අතර පිටත ස්ථරයේ ඉරිතැලීම් ඇත. බරපතල අවස්ථාවන්හිදී, ලෝහයේ අඛණ්ඩතාව බරපතල ලෙස හානි කරනු ඇත.නිස්සාරණ ක්රියාවලියේදී ඩයි බිත්තියේ අධික ආවර්තිතා ආතන්ය ආතතියෙන් ලෝහ මතුපිට ඉරා දැමූ විට නිස්සාරණ ඉරිතැලීම් සෑදී ඇත.
නිස්සාරණය ඉරිතැලීම් සඳහා ප්රධාන හේතුව
1. නිස්සාරණ වේගය ඉතා වේගවත් ය;
2. පිටකිරීමේ උෂ්ණත්වය ඉතා ඉහළ ය;
3. නිස්සාරණ වේගය අධික ලෙස උච්චාවචනය වේ;
4. නිස්සාරණය කරන ලද ලොම්වල උෂ්ණත්වය ඉතා ඉහළ ය;
5. සිදුරු සහිත ඩයි නිස්සාරණය කරන විට, මධ්ය ලෝහ සැපයුම ප්රමාණවත් නොවන පරිදි, මධ්යයේ සහ දාර ප්රවාහ අනුපාතය අතර වෙනස ඉතා විශාල වන පරිදි, මිය යන සැකැස්ම මධ්යයට ඉතා සමීප වේ;
6. ingot homogenization annealing හොඳ නැත.
වැළැක්වීමේ ක්රමය
1. විවිධ උනුසුම් සහ නිස්සාරණ පිරිවිතර දැඩි ලෙස ක්රියාත්මක කිරීම;
2. සාමාන්ය ක්රියාකාරීත්වය සහතික කිරීම සඳහා උපකරණ සහ උපකරණ නිතර නිතර පරීක්ෂා කිරීම;
3. අච්චු නිර්මාණය වෙනස් කිරීම සහ එය ප්රවේශමෙන් සකසන්න, විශේෂයෙන් අච්චු පාලම, වෙල්ඩින් කාමරය සහ දාර අරය ආදියෙහි සැලසුම සාධාරණ විය යුතුය;
4. ඉහළ මැග්නීසියම් ඇලුමිනියම් මිශ්ර ලෝහවල සෝඩියම් අන්තර්ගතය අවම කිරීම;
5. එහි ප්ලාස්ටික් බව සහ ඒකාකාරිත්වය වැඩි දියුණු කිරීම සඳහා ඉන්ගෝට් සමජාතීය කර ඇත.
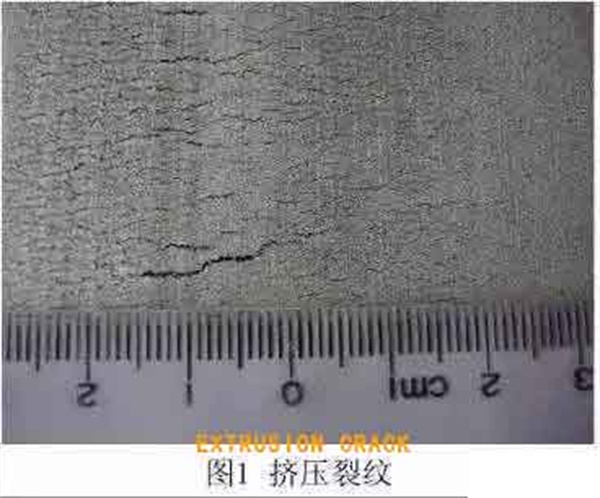
VIබුබුලු
දේශීය සමේ ලෝහය පාදක ලෝහයෙන් අඛණ්ඩව හෝ අඛණ්ඩව වෙන් වී ඇති අතර, එය බුබුලක් ලෙස හඳුන්වන වෘත්තාකාර තනි හෝ තීරු හැඩැති කුහරයක් මතු වූ දෝෂයක් ලෙස ප්රකාශ වේ.
බුබුලු ඇතිවීමට ප්රධාන හේතුව
1. නිස්සාරණය කරන විට, නිස්සාරණ සිලින්ඩරය සහ පිටකිරීමේ පෑඩ් තෙතමනය හා තෙල් වැනි අපිරිසිදුකම් ඇත;
2. නිස්සාරණ සිලින්ඩරයේ ඇඳීම හේතුවෙන්, අඳින ලද කොටස සහ ඉන්ගෝට් අතර වාතය නිස්සාරණය කිරීමේදී ලෝහ මතුපිටට ඇතුල් වේ;
3. ලිහිසි තෙල් තුළ තෙතමනය පවතී;
4. ඉන්ගෝට් ව්යුහයේම ලිහිල් හා සිදුරු සහිත දෝෂ ඇත;
5. තාප පිරියම් කිරීමේ උෂ්ණත්වය ඉතා ඉහළ ය, රැඳවුම් කාලය ඉතා දිගු වන අතර උදුනෙහි වායුගෝලීය ආර්ද්රතාවය ඉහළ ය;
6. නිෂ්පාදනයේ හයිඩ්රජන් අන්තර්ගතය ඉතා ඉහළ ය;
7. Extrusion සිලින්ඩර උෂ්ණත්වය සහ ingot උෂ්ණත්වය ඉතා ඉහළ ය.
වැළැක්වීමේ ක්රමය
1. මෙවලම් සහ ඉන්ගෝට් මතුපිට පිරිසිදු, සිනිඳු සහ වියලි ලෙස තබා ගත යුතුය;
2. නිස්සාරණ සිලින්ඩරයේ සහ නිස්සාරණ ගෑස්කට් එකට ගැලපෙන ප්රමාණය සාධාරණ ලෙස සැලසුම් කරන්න, මෙවලමෙහි ප්රමාණය නිතර පරීක්ෂා කරන්න, විශාල බඩක් ඇති විට නිස්සාරණ සිලින්ඩරය අලුත්වැඩියා කරන්න, සහ නිස්සාරණ ගෑස්කට් ඉවසීමෙන් බැහැර නොවිය යුතුය;
3. ලිහිසි තෙල් පිරිසිදු හා වියලි බව සහතික කරන්න;
4. නිස්සාරණ ක්රියාවලි මෙහෙයුම් ක්රියාවලියට දැඩි ලෙස පිළිපදින්න, නියමිත වේලාවට පිටාර ගැලීම, නිවැරදිව කපන්න, තෙල් ආලේප නොකරන්න, අවශේෂ ද්රව්ය සම්පූර්ණයෙන්ම ඉවත් කරන්න, හිස් තැන් සහ අච්චු පිරිසිදුව තබා ගන්න.
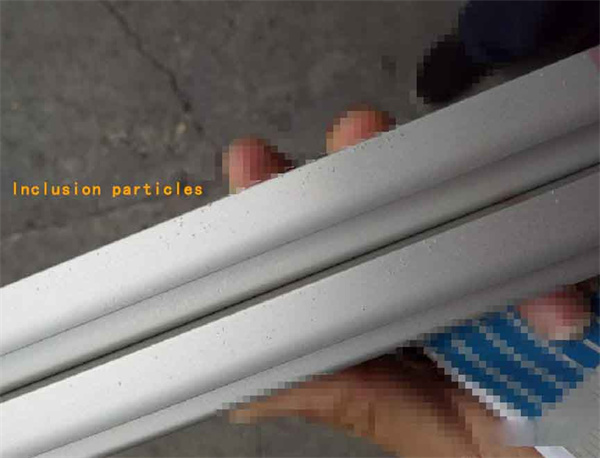
VII.පීල් කිරීම
ඇලුමිනියම් මිශ්ර ලෝහ නිස්සාරණ නිෂ්පාදනයේ සමේ ලෝහය සහ මූලික ලෝහය අතර දේශීය වෙන්වීමේ සංසිද්ධිය මෙයයි.
පීල් කිරීමේ ප්රධාන හේතුව
1. මිශ්ර ලෝහය ප්රතිස්ථාපනය කර නිස්සාරණය කරන විට, නිස්සාරණ සිලින්ඩරයේ අභ්යන්තර බිත්තිය නිසි ලෙස පිරිසිදු නොකළ මුල් ලෝහයෙන් සාදන ලද බුෂ් වෙත ඇලී තිබේ;
2. නිස්සාරණ සිලින්ඩරය සහ නිස්සාරණ පෑඩය නිසියාකාරව නොගැලපෙන අතර, නිස්සාරණ සිලින්ඩරයේ අභ්යන්තර බිත්තිය දේශීය අවශේෂ ලෝහවලින් ආවරණය කර ඇත;
3. එය ලිහිසි කරන නිස්සාරණ සිලින්ඩරය මගින් නෙරා ඇත;
4. ඩයි කුහරයේ ලෝහයක් තිබේ හෝ ඩයි එකේ වැඩ කරන පටිය දිගු වේ.
වැළැක්වීමේ ක්රමය
1. මිශ්ර ලෝහය නිස්සාරණය කිරීමේදී නිස්සාරණ සිලින්ඩරය හොඳින් පිරිසිදු කරන්න;
2. නිස්සාරණ සිලින්ඩරයේ සහ නිස්සාරණ ගෑස්කට් එකට ගැලපෙන ප්රමාණය සාධාරණ ලෙස සැලසුම් කරන්න, මෙවලම් ප්රමාණය නිතර පරීක්ෂා කරන්න, සහ නිස්සාරණ ගෑස්කට් ඉවසීමෙන් බැහැර විය නොහැක;
3. නියමිත වේලාවට අච්චුවේ ඉතිරි ලෝහ පිරිසිදු කරන්න.
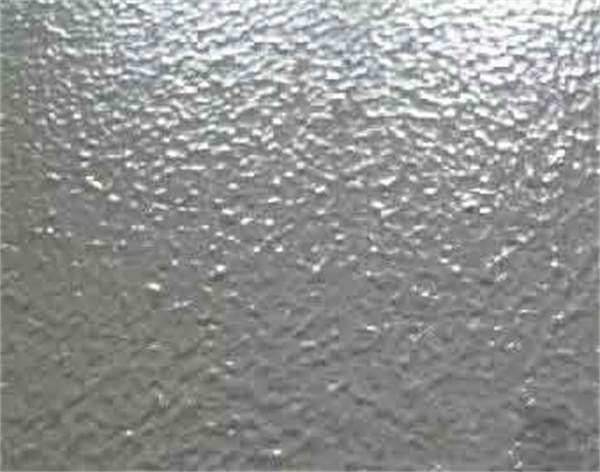
VIII.සීරීම්
සාපේක්ෂ ලිස්සා යාමේදී තියුණු වස්තූන් සහ නිෂ්පාදනයේ මතුපිට අතර ස්පර්ශය නිසා ඇතිවන තනි ඉරි සහිත යාන්ත්රික කැළැල් සීරීම් ලෙස හැඳින්වේ.
සීරීම් සඳහා ප්රධාන හේතුව
1. මෙවලම් වැරදි එකලස් කිරීම, නොගැලපෙන මාර්ගෝපදේශ සහ වැඩ වගු, තියුණු කොන් හෝ විදේශීය වස්තූන් ආදිය.
2. අච්චුව වැඩ කරන පටිය මත ලෝහ චිප්ස් ඇත හෝ අච්චුව වැඩ කරන පටිය හානි වේ;
3. ලිහිසි තෙල්වල වැලි හෝ කැඩුණු ලෝහ චිප්ස් ඇත;
4. ප්රවාහනයේදී අනිසි ලෙස ක්රියා කිරීම සහ නුසුදුසු පැතිරීම.
වැළැක්වීමේ ක්රමය
1. නියමිත වේලාවට අච්චුව වැඩ කරන පටිය පරීක්ෂා කර ඔප දමන්න;
2. නිෂ්පාදනයේ පිටතට ගලා යන නාලිකාව පරීක්ෂා කරන්න, එය සුමට විය යුතු අතර, මාර්ගෝපදේශ මාර්ගය නිසි ලෙස ලිහිසි කළ හැක;
3. හැසිරවීමේදී යාන්ත්රික අතුල්ලමින් හා සීරීම් වැළැක්වීම.
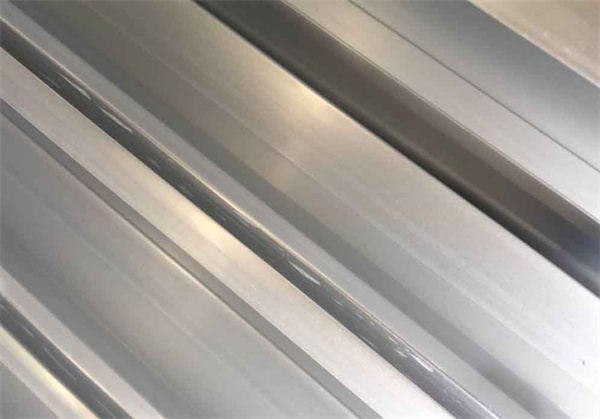
IX.ගැටිති
නිෂ්පාදනවල මතුපිට ඇති වූ කැළැල් හෝ වෙනත් වස්තූන් සමඟ ගැටුණු නිෂ්පාදන ගැටිති තුවාල ලෙස හැඳින්වේ.
ගැටිති ඇතිවීමට ප්රධාන හේතුව
1. වැඩ බංකුව සහ ද්රව්ය රාක්කයේ ව්යුහය අසාධාරණ ය;
2. ද්රව්ය බාස්කට්, ද්රව්ය රාක්ක, ආදිය වැරදි ෙලෝහ ආරක්ෂණය;
3. ක්රියාත්මක වන විට එය ප්රවේශමෙන් හසුරුවන්න එපා.
වැළැක්වීමේ ක්රමය
1. ප්රවේශමෙන් ක්රියා කිරීම, ප්රවේශමෙන් හැසිරවීම;
2. තියුණු කොන් ඇඹරීමට, කූඩය සහ රාක්කය ඩන්ජ් සහ මෘදු ද්රව්යවලින් ආවරණය කරන්න.
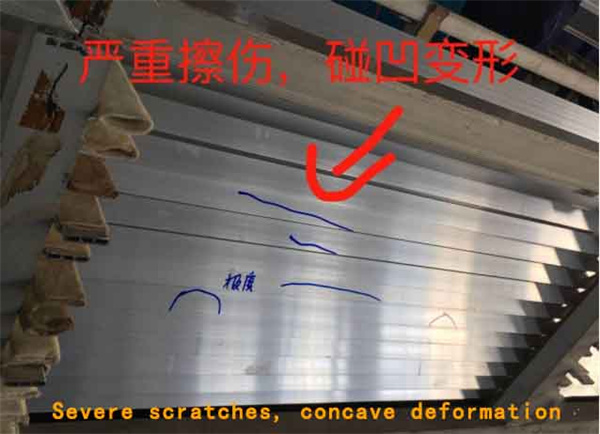
X. සීරීම්
නිස්සාරණය කරන ලද නිෂ්පාදනයේ මතුපිට වෙනත් වස්තූන්ගේ දාර හෝ මතුපිට ස්පර්ශ වීමෙන් පසු සාපේක්ෂ ලිස්සා යාම හෝ විස්ථාපනය හේතුවෙන් නිෂ්පාදනයේ මතුපිට මිටි ලෙස බෙදා හරින ලද කැළැල් සීරීම් ලෙස හැඳින්වේ.
සීරීම් සඳහා ප්රධාන හේතුව
1. අච්චුව බරපතල ලෙස පැළඳ සිටී;
2. ඉන්ගෝට් වල අධික උෂ්ණත්වය හේතුවෙන්, ඩයි කුහරය ඇලුමිනියම් වලට ඇලී සිටීම හෝ ඩයි කුහරය වැඩ කරන පටියට හානි වේ;
3. ග්රැෆයිට් සහ තෙල් වැනි අපිරිසිදුකම නිස්සාරණ සිලින්ඩරයට වැටේ;
4. නිෂ්පාදන එකිනෙක චලනය වන අතර එමඟින් මතුපිට සීරීම් සහ නිස්සාරණ ප්රවාහය අසමාන වන අතර එමඟින් නිෂ්පාදන සරල රේඛාවකින් ගලා නොයෑමට හේතු වන අතර එමඟින් ද්රව්යය සහ මාර්ගෝපදේශ මාර්ගය සහ වැඩ මේසය අතර සීරීම් ඇති වේ.
වැළැක්වීමේ ක්රමය
1. නියමිත වේලාවට නුසුදුසු අච්චු පරීක්ෂා කර ප්රතිස්ථාපනය කරන්න;
2. ලොම් තාපන උෂ්ණත්වය පාලනය කරන්න;
3. නිස්සාරණ සිලින්ඩරයේ සහ ලොම්වල මතුපිට පිරිසිදු හා වියලි බව සහතික කිරීම;
4. ඒකාකාර වේගය සහතික කිරීම සඳහා නිස්සාරණ වේගය පාලනය කරන්න.
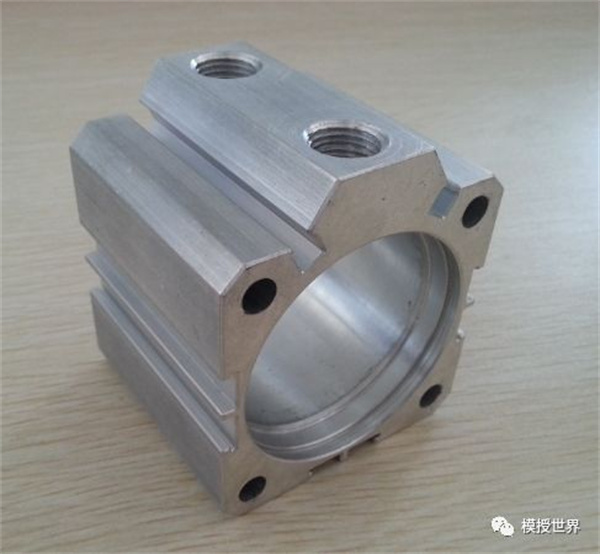
XI.අච්චු සලකුණු
මෙය නිස්සාරණය කරන ලද නිෂ්පාදනයේ මතුපිට කල්පවත්නා අසමානතාවයේ හෝඩුවාවක් වන අතර, සියලුම නිස්සාරණය කරන ලද නිෂ්පාදනවල විවිධ මට්ටම් වලට මිය යන ලකුණු ඇත.
පුස් සලකුණු ප්රධාන හේතුව
ප්රධාන හේතුව: අච්චුව වැඩ කරන පටිය නිරපේක්ෂ සුමටතාවය ලබා ගත නොහැක.
වැළැක්වීමේ ක්රමය
1. අච්චුව වැඩ කරන පටියේ මතුපිට පිරිසිදු, සිනිඳු සහ තියුණු දාරවලින් තොර බව සහතික කර ගන්න;
2. ඉහළ මතුපිට දෘඪතාව සහතික කිරීම සඳහා සාධාරණ නයිට්රයිඩින් ප්රතිකාරය;
3. අච්චුව නිවැරදිව අලුත්වැඩියා කරන්න;
4. වැඩ කරන පටිය සාධාරණ ලෙස නිර්මාණය කළ යුතු අතර, වැඩ කරන පටිය දිගු නොවිය යුතුය.
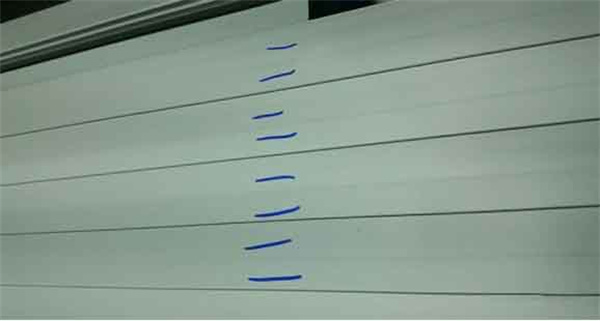
XII.ඇඹරීම, නැමීම, රැල්ල
නිස්සාරණය කරන ලද නිෂ්පාදනයේ හරස්කඩ කල්පවත්නා දිශාවට කෝණික ලෙස අපගමනය වන සංසිද්ධිය twisting ලෙස හැඳින්වේ.නිෂ්පාදිතය කල්පවත්නා දිශාවට වක්ර වීම හෝ පිහියේ හැඩය කෙළින් නොවීම යන සංසිද්ධිය නැමීම ලෙස හැඳින්වේ.නිෂ්පාදනයේ කල්පවත්නා දිශාවට සිදුවන අඛණ්ඩ රැලි සහිත සංසිද්ධිය තරංගයක් ලෙස හැඳින්වේ.
ඇඹරීම, නැමීම සහ තරංගවල ප්රධාන හේතු
1. ඩයි කුහරවල සැලසුම සහ සැකැස්ම හොඳ නැත, නැතහොත් වැඩ කරන පටියේ ප්රමාණය බෙදා හැරීම අසාධාරණ ය;
2. ඩයි කුහරවල දුර්වල යන්ත්ර නිරවද්යතාවය;
3. නිසි මාර්ගෝපදේශය ස්ථාපනය කර නැත;
4. නුසුදුසු අච්චු අලුත්වැඩියා කිරීම;
5. නුසුදුසු නිස්සාරණ උෂ්ණත්වය සහ වේගය;
6. ද්රාවණය ප්රතිකාර කිරීමට පෙර නිෂ්පාදිතය පූර්ව සෘජු කර නැත;
7. අන්තර්ජාල තාප පිරියම් කිරීමේදී අසමාන සිසිලනය.
වැළැක්වීමේ ක්රමය
1. ඉහළ මට්ටමේ අච්චු නිර්මාණය සහ නිෂ්පාදනය;
2. සුදුසු මාර්ගෝපදේශයක්, කම්පන සහ නිස්සාරණය ස්ථාපනය කරන්න;
3. ෙලෝහමය ගලන අනුපාතය සකස් කිරීම සඳහා ෙද්ශීය ලිහිසි කිරීම, පුස් අළුත්වැඩියා කිරීම සහ හැරවීම භාවිතා කිරීම ෙහෝ ෂන්ට් කුහරය සැලසුම් කිරීම ෙවනස් කිරීම;
4. විරූපණය වඩාත් ඒකාකාරී කිරීම සඳහා නිස්සාරණ උෂ්ණත්වය සහ වේගය සාධාරණ ලෙස සකස් කරන්න;
5. විසඳුම ප්රතිකාර උෂ්ණත්වය සුදුසු ලෙස අඩු කිරීම හෝ විසඳුම ප්රතිකාර සඳහා ජල උෂ්ණත්වය වැඩි කිරීම;
6. සබැඳි නිවාදැමීමේදී ඒකාකාර සිසිලනය සහතික කරන්න.
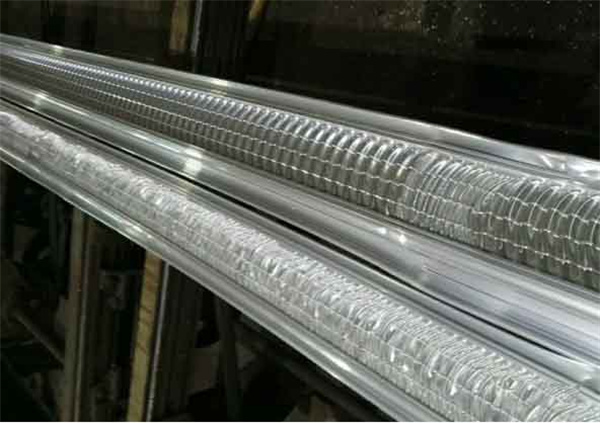
XIII.දැඩි වංගුව
දිගු දිශාවට කොහේ හරි නිස්සාරණය කරන ලද නිෂ්පාදනයක් හදිසියේ නැමීම දෘඪ වංගුව ලෙස හැඳින්වේ.
දැඩි නැමීමේ ප්රධාන හේතුව
1. අසමාන නිස්සාරණ වේගය, අඩු වේගයේ සිට අධික වේගය දක්වා හදිසි වෙනස් වීම හෝ අධික වේගයේ සිට අඩු වේගය දක්වා හදිසි වෙනස් වීම සහ හදිසි නැවතුම;
2. නිස්සාරණ ක්රියාවලියේදී නිෂ්පාදිතය තදින් චලනය කරන්න;
3. extruder වැඩ කරන පෘෂ්ඨය අසමාන වේ.
වැළැක්වීමේ ක්රමය
1. අහඹු ලෙස නතර නොකරන්න හෝ නිස්සාරණ වේගය හදිසියේ වෙනස් නොකරන්න;
2. පැතිකඩ හදිසියේ අතින් ගෙන නොයන්න;
3. විසර්ජන වගුව පැතලි බවත්, විසර්ජන රෝලර් වගුව විදේශීය ද්රව්ය නොමැතිව සුමට බවත්, ඒකාබද්ධ නිෂ්පාදනය බාධාවකින් තොරව බවත් සහතික කර ගන්න.
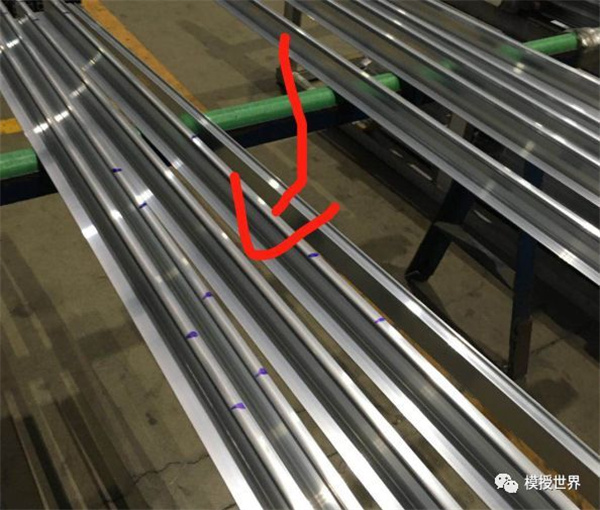
XIV.කංසා නූඩ්ල්ස්
මෙය නිස්සාරණය කරන ලද නිෂ්පාදනයේ මතුපිට දෝෂය වන අතර එයින් අදහස් කරන්නේ නිෂ්පාදනයේ මතුපිට අඛණ්ඩ පෙති, පැල්ලම් සීරීම්, වලවල්, ලෝහ බෝංචි ආදිය කුඩා අසමානතාවයකින් බවයි.
pockmark ඇතිවීමට ප්රධාන හේතුව
1. අච්චුවේ දෘඪතාව ප්රමාණවත් නොවේ හෝ දෘඪතාව අසමාන වේ;
2. පිටකිරීමේ උෂ්ණත්වය ඉතා ඉහළ ය;
3. නිස්සාරණ වේගය ඉතා වේගවත් ය;
4. අච්චුවේ වැඩ කරන පටිය ඉතා දිගු, රළු හෝ ලෝහ සමග සිරවී ඇත;
5. නෙරා ඇති ලොම් ඉතා දිගු වේ.
වැළැක්වීමේ ක්රමය
1. අච්චුව වැඩ කරන පටියෙහි දෘඪතාව සහ දෘඪතාව ඒකාකාරිත්වය වැඩි දියුණු කිරීම;
2. රෙගුලාසිවලට අනුව නිස්සාරණ සිලින්ඩරය සහ ඉන්ගෝට් රත් කර සුදුසු නිස්සාරණ වේගය භාවිතා කරන්න;
3. සාධාරණ ලෙස අච්චුව සැලසුම් කිරීම, වැඩ කරන තීරයේ මතුපිට රළුබව අඩු කිරීම සහ මතුපිට පරීක්ෂා කිරීම, අලුත්වැඩියා කිරීම සහ ඔප දැමීම ශක්තිමත් කිරීම;
4. සාධාරණ ඉන්ගෝට් දිගක් භාවිතා කරන්න.
XV.ලෝහ පීඩනය
නිස්සාරණය කිරීමේ ක්රියාවලියේදී, ලෝහ චිප්ස් නිෂ්පාදනයේ මතුපිටට තද කරනු ලැබේ, එය ලෝහ පීඩනය ලෙස හැඳින්වේ.
ලෝහ ආක්රමණයේ ප්රධාන හේතු:
1. ලොම් කෙළවර දෝෂ සහිතයි;
2. ලොම් අභ්යන්තර මතුපිට ලෝහ සමග සිරවී හෝ ලිහිසි තෙල් ලෝහ සුන්බුන් සහ අනෙකුත් අපිරිසිදු අඩංගු වේ;
3. නිස්සාරණ සිලින්ඩරය පිරිසිදු කර නොමැති අතර, වෙනත් ලෝහ සුන්බුන් ඇත;
4. ඉන්ගෝට් වෙනත් ලෝහමය විදේශීය වස්තූන් තුළට ගිල්වනු ලැබේ;
5. ලොම්වල ස්ලැග් ඇතුළත් කිරීමක් ඇත.
වැළැක්වීමේ ක්රමය
1. ලොම් මත බර්ස් ඉවත් කරන්න;
2. ලොම් මතුපිට සහ ලිහිසි තෙල් පිරිසිදු හා වියලි බව සහතික කර ගන්න;
3. අච්චු සහ නිස්සාරණ සිලින්ඩරයේ ලෝහ සුන්බුන් පිරිසිදු කරන්න;
4. උසස් තත්ත්වයේ ලොම් තෝරන්න.
XVI.ලෝහ නොවන පීඩනය
ගල් කළු වැනි ආගන්තුක ද්රව්ය නිස්සාරණය කරන ලද නිෂ්පාදනයේ අභ්යන්තර හා පිටත පෘෂ්ඨවලට තද කරනු ලැබේ, එය ලෝහමය නොවන ඉන්ඩෙන්ටේෂන් ලෙස හැඳින්වේ.විදේශීය ද්රව්ය ඉවත් කිරීමෙන් පසුව, නිෂ්පාදනයේ අභ්යන්තර පෘෂ්ඨය විවිධ ප්රමාණවලින් අවපාතයන් පෙන්වනු ඇත, නිෂ්පාදනයේ මතුපිට අඛණ්ඩතාව විනාශ කරනු ඇත.
ලෝහමය නොවන ආක්රමණයේ ප්රධාන හේතුව
1. මිනිරන් අංශු ප්රමාණය රළු හෝ සමුච්චිත, තෙතමනය හෝ තෙල් අඩංගු වන අතර ඇවිස්සීම අසමාන වේ;
2. සිලින්ඩර තෙල්වල ෆ්ලෑෂ් පොයින්ට් අඩුයි;
3. සිලින්ඩර තෙල් සහ මිනිරන් අනුපාතය නුසුදුසු වන අතර, මිනිරන් වැඩියි.
වැළැක්වීමේ ක්රමය
1. සුදුසුකම් ලත් මිනිරන් භාවිතා කර එය වියළිව තබා ගන්න;
2. සුදුසුකම් ලත් ලිහිසි තෙල් පෙරීම සහ භාවිතා කිරීම;
3. ලිහිසි තෙල් සහ මිනිරන් අනුපාතය පාලනය කරන්න.
XVII.මතුපිට විඛාදනය
පෘෂ්ඨීය ප්රතිකාරයට ලක් නොවූ නිස්සාරණය කරන ලද නිෂ්පාදන, බාහිර මාධ්ය සමඟ රසායනික හෝ විද්යුත් රසායනික ප්රතික්රියාවෙන් පසු නිස්සාරණය කරන ලද නිෂ්පාදනයේ මතුපිට, මතුපිට විඛාදනය ලෙස හැඳින්වෙන මතුපිට දේශීය හානිය නිසා ඇති වන දෝෂය ඇති කරයි.විඛාදනයට ලක් වූ නිෂ්පාදනයේ මතුපිට එහි ලෝහමය දීප්තිය නැති වී යන අතර දරුණු අවස්ථාවල දී අළු-සුදු විඛාදන නිෂ්පාදන මතුපිටින් නිපදවනු ලැබේ.
මතුපිට විඛාදනයට ප්රධාන හේතුව
1. නිෂ්පාදිතය, නිෂ්පාදනය, ගබඩා කිරීම සහ ප්රවාහනය කිරීමේදී ජලය, අම්ලය, ක්ෂාර, ලුණු වැනි විඛාදන මාධ්යවලට නිරාවරණය වේ, නැතහොත් දිගු කාලයක් තෙත් වායුගෝලයේ නවතා ඇත;
2. නුසුදුසු මිශ්ර ලෝහ සංයුතිය අනුපාතය;
වැළැක්වීමේ ක්රමය
1. නිෂ්පාදන මතුපිට සහ නිෂ්පාදන සහ ගබඩා පරිසරය පිරිසිදු හා වියලි තබා ගන්න;
2. මිශ්ර ලෝහයේ මූලද්රව්යවල අන්තර්ගතය පාලනය කරන්න.
XVIII.තැඹිලි පීල්
නිස්සාරණය කරන ලද නිෂ්පාදනයේ මතුපිට තැඹිලි ලෙලි වැනි අසමාන රැලි ඇත, එය මතුපිට රැලි ලෙසද හැඳින්වේ.එය නිස්සාරණය කිරීමේදී රළු ධාන්ය මගින් ඇතිවේ.ගොරෝසු ධාන්ය, වඩාත් පැහැදිලිව රැලි.
දොඩම් ලෙලි ඇතිවීමට ප්රධාන හේතුව
1. ඉන්ගෝට් ව්යුහය අසමාන වන අතර සමජාතීය ප්රතිකාරය ප්රමාණවත් නොවේ;
2. නිස්සාරණ කොන්දේසි අසාධාරණ වන අතර, නිමි භාණ්ඩවල ධාන්ය රළු වේ;
3. දිගු කිරීම සහ සෘජු කිරීම ප්රමාණය ඉතා විශාලය.
වැළැක්වීමේ ක්රමය
1. සමජාතීය කිරීමේ ක්රියාවලිය සාධාරණ ලෙස පාලනය කිරීම;
2. විරූපණය හැකි තරම් ඒකාකාරී විය යුතුය (නිස්සාරණ උෂ්ණත්වය, වේගය, ආදිය පාලනය කරන්න)
3. ආතති නිවැරදි කිරීමේ ප්රමාණය ඉතා විශාල නොවන ලෙස පාලනය කරන්න.
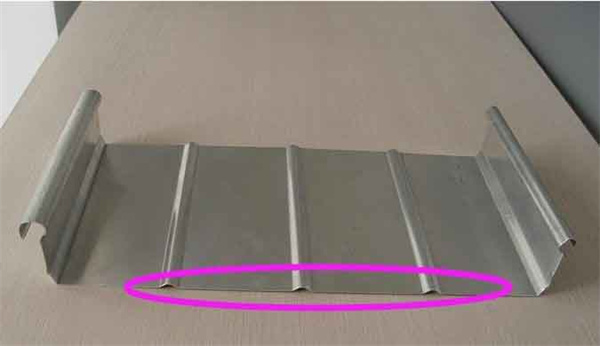
XIX.අසමාන
නිස්සාරණයෙන් පසුව, තලය මත නිෂ්පාදනයේ ඝනකම වෙනස් වන ප්රදේශය අවතල හෝ උත්තල ලෙස පෙනේ.සාමාන්යයෙන් එය පියවි ඇසින් නිරීක්ෂණය කළ නොහැක.මතුපිට ප්රතිකාර කිරීමෙන් පසු සිහින් සෙවනැලි හෝ අස්ථි සෙවනැලි පෙනේ.
අසමානතාවයේ ප්රධාන හේතුව
1. අච්චුව වැඩ කරන පටිය නිසියාකාරව නිර්මාණය කර නොමැති අතර, අච්චු අලුත්වැඩියා කිරීම සිදු නොවේ;
2. ෂන්ට් කුහරයේ හෝ පෙර කුටීරයේ විශාලත්වය සුදුසු නොවන අතර, හරස් ප්රදේශයෙහි පැතිකඩ ඇදගෙන යාමේ හෝ පුළුල් කිරීමේ බලය ගුවන් යානයේ සුළු වෙනසක් ඇති කරයි;
3. සිසිලන ක්රියාවලිය අසමාන වන අතර, ඝන-බිත්ති කොටස හෝ ඡේදනය වන කොටසෙහි සිසිලන වේගය මන්දගාමී වේ, සිසිලන ක්රියාවලියේදී ගුවන් යානයේ විවිධ මට්ටම් හැකිලීම සහ විරූපණය වීම;
4. ඝනකමේ දැවැන්ත වෙනස හේතුවෙන් ඝන බිත්ති සහිත කොටස හෝ සංක්රාන්ති ප්රදේශය සංවිධානය කිරීම සහ සංවිධානයේ අනෙකුත් කොටස් අතර වෙනස වැඩි වේ.
වැළැක්වීමේ ක්රමය
1. අච්චු නිර්මාණය, නිෂ්පාදනය සහ අච්චු අලුත්වැඩියා මට්ටම වැඩි දියුණු කිරීම;
2. ඒකාකාර සිසිලන වේගය සහතික කිරීම.
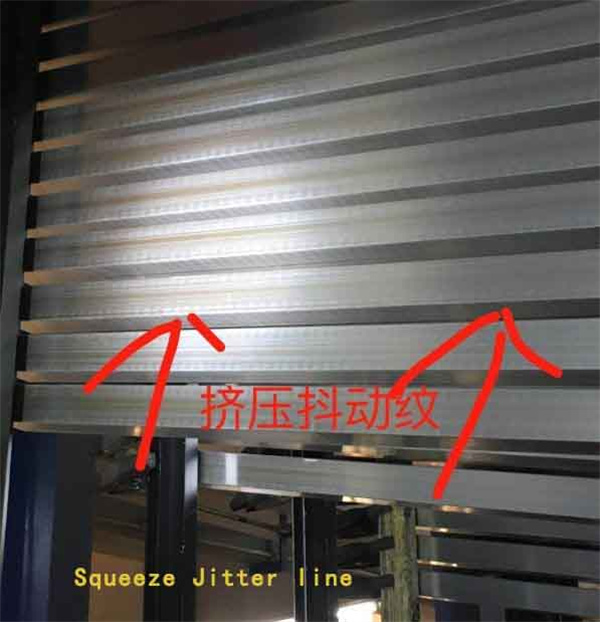
XX.කම්පන රටාව
මෙය නිස්සාරණය කරන ලද නිෂ්පාදනයේ මතුපිටට හරස් අතට ආවර්තිතා ඉරි දෝෂයකි.එය නිෂ්පාදනයේ මතුපිට තිරස් අඛණ්ඩ ආවර්තිතා ඉරි මගින් සංලක්ෂිත වන අතර, තීරු වක්රය අච්චුවේ වැඩ කරන පටියේ හැඩයට අනුකූල වන අතර බරපතල අවස්ථාවන්හිදී, පැහැදිලි ගැටිති හැඟීමක් ඇත.
කම්පනයට ප්රධාන හේතුව
1. නිස්සාරණ පතුවළ ඉදිරියට ගමන් කරන අතර උපකරණ හේතූන් නිසා සෙලවෙන අතර, එය කුහරයෙන් පිටතට ගලා යන විට ලෝහය සෙලවීමට හේතු වේ;
2. අච්චුව හේතුවෙන් ඩයි කුහරයෙන් පිටතට ගලා යන විට ලෝහය සෙලවේ;
3. අච්චු ආධාරක පෑඩය සුදුසු නොවේ, අච්චුවේ දෘඪතාව හොඳ නැත, සහ පිටකිරීමේ බලය උච්චාවචනය වන විට කම්පනය සිදු වේ.
වැළැක්වීමේ ක්රමය
1. සුදුසුකම් ලත් අච්චු භාවිතා කරන්න;
2. අච්චුව ස්ථාපනය කරන විට සුදුසු ආධාරක පෑඩ් භාවිතා කළ යුතුය;
3. උපකරණ සකස් කරන්න.
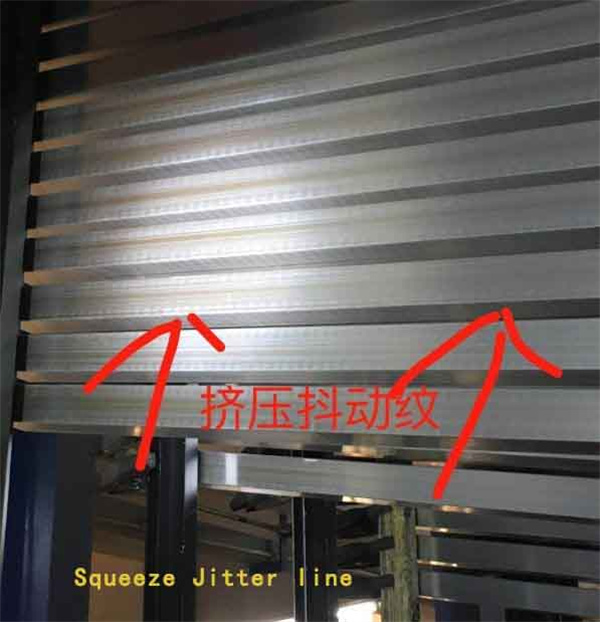
XXI, මිශ්ර
ඇතුළත් කිරීම් සඳහා ප්රධාන හේතුව
ඇතුළත් කිරීමේ බිල්ට්ටුවේ ලෝහ හෝ ලෝහ නොවන ඇතුළත් කිරීම් ඇති බැවින්, එය පෙර ක්රියාවලියේදී හමු නොවූ අතර, නිස්සාරණයෙන් පසු නිෂ්පාදනයේ මතුපිට හෝ ඇතුළත පැවතුනි.
වැළැක්වීමේ ක්රමය
ලෝහ හෝ ලෝහමය නොවන ඇතුළත් කිරීම් සහිත බිල්පත් නිස්සාරණ ක්රියාවලියට ඇතුල් වීම වැළැක්වීම සඳහා බිල්ට් (අතිධ්වනික පරීක්ෂාව ඇතුළුව) පරීක්ෂා කිරීම ශක්තිමත් කරන්න.

XXII, ජල සලකුණු
නිෂ්පාදනයේ මතුපිට ඇති ලා සුදු හෝ ලා කළු අක්රමවත් ජල මාර්ග සලකුණු ජල සලකුණු ලෙස හැඳින්වේ.
ජල සලකුණු ඇතිවීමට ප්රධාන හේතුව
1. පිරිසිදු කිරීමෙන් පසු වියළීම හොඳ නැත, නිෂ්පාදනයේ මතුපිට ඉතිරි තෙතමනය පවතී;
2. වර්ෂාපතනය සහ වෙනත් හේතූන් නිසා ඇති වූ නිෂ්පාදනයේ මතුපිට ඉතිරි තෙතමනය නියමිත වේලාවට පිරිසිදු කර නොමැත;
3. වයෝවෘද්ධ උදුනෙහි ඉන්ධන ජලය අඩංගු වන අතර, වයසට යාමෙන් පසු නිෂ්පාදනයේ සිසිලනය තුළ නිෂ්පාදනයේ මතුපිට ජලය ඝනීභවනය වේ;
4. වයසට යෑමේ උදුනේ ඉන්ධන පිරිසිදු නොවන අතර, නිෂ්පාදනයේ මතුපිට දහනය කිරීමෙන් හෝ දූවිලි වලින් දූෂිත වීමෙන් පසු සල්ෆර් ඩයොක්සයිඩ් මගින් විඛාදනයට ලක් වේ;
5. නිවන මාධ්යය දූෂණය වේ.
වැළැක්වීමේ ක්රමය
1. නිෂ්පාදනයේ මතුපිට වියළි හා පිරිසිදුව තබා ගන්න;
2. වයස්ගත ආරෝපණයේ තෙතමනය හා පිරිසිදුකම පාලනය කිරීම;
3. නිවාදැමීමේ මාධ්ය කළමනාකරණය ශක්තිමත් කිරීම.
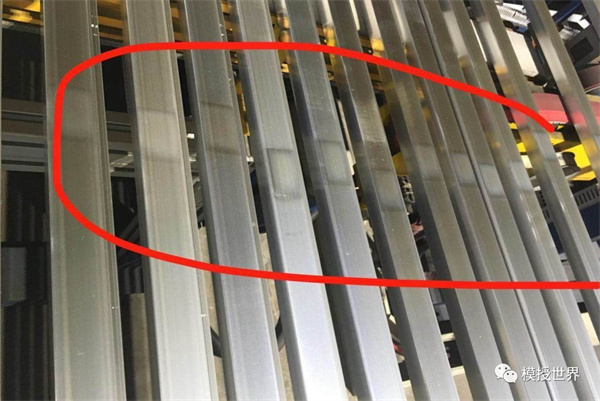
XXIII.පරතරය
නිස්සාරණය කරන ලද නිෂ්පාදනයේ යම් තලයක් මත පාලකය තිරස් අතට අධිස්ථාපනය කර ඇති අතර, පාලකය සහ මතුපිට අතර යම් පරතරයක් ඇති අතර එය පරතරයක් ලෙස හැඳින්වේ.
පරතරයේ ප්රධාන හේතුව
නිස්සාරණය හෝ නුසුදුසු නිමාව සහ සෘජු කිරීමේ මෙහෙයුම් වලදී අසමාන ලෝහ ප්රවාහය.
වැළැක්වීමේ ක්රමය
සාධාරණ ලෙස අච්චු සැලසුම් කිරීම සහ නිෂ්පාදනය කිරීම, අච්චු අලුත්වැඩියාව ශක්තිමත් කිරීම සහ නිස්සාරණයේ උෂ්ණත්වය සහ නිස්සාරණ වේගය පාලනය කිරීම සඳහා දැඩි රෙගුලාසි වලට අනුකූලව.
XXIV, අසමාන බිත්ති ඝණකම
එකම ප්රමාණයේ නිස්සාරණ නිෂ්පාදන එකම කොටසේ හෝ කල්පවත්නා දිශාවකින් තුනී හෝ ඝන බිත්ති ඇති අතර සංසිද්ධිය අසමාන බිත්ති ඝණත්වය ලෙස හැඳින්වේ.
අසමාන බිත්ති ඝණකම ප්රධාන හේතුව
1. අච්චු නිර්මාණය අසාධාරණ ය, නැතහොත් මෙවලම සහ අච්චු එකලස් කිරීම නුසුදුසු ය;
2. නිස්සාරණ සිලින්ඩරය සහ නිස්සාරණ ඉඳිකටුවක් එකම මධ්ය රේඛාවක් මත නොපවතින අතර, විකේන්ද්රියතාව සාදයි;
3. නිස්සාරණ සිලින්ඩරයේ ආස්තරය අධික ලෙස අඳිනු ලබන අතර, අච්චුව තදින් සවි කළ නොහැකි අතර, එහි ප්රතිඵලයක් වශයෙන් විකේන්ද්රිකතාවය ඇති වේ;
4. පළමු හා දෙවන නිස්සාරණයෙන් පසු ඉන්ගෝට් හිස් වල අසමාන බිත්ති ඝණත්වය ඉවත් කළ නොහැක.නිස්සාරණයෙන් පසු ලොම්වල අසමාන බිත්ති ඝණත්වය පෙරළීමෙන් හා දිගු කිරීමෙන් පසු ඉවත් නොකෙරේ;
5. ලිහිසි තෙල් අසමාන ලෙස යොදන අතර එමඟින් ලෝහය අසමාන ලෙස ගලා යයි.
වැළැක්වීමේ ක්රමය
1. මෙවලම් සහ අච්චු සැලසුම් කිරීම සහ නිෂ්පාදනය කිරීම ප්රශස්ත කිරීම සහ තාර්කිකව එකලස් කිරීම සහ සකස් කිරීම;
2. extruder සහ extrusion die කේන්ද්රය සකස් කරන්න;
3. සුදුසුකම් ලත් හිස් තැන් තෝරන්න;
4. නිස්සාරණ උෂ්ණත්වය, නිස්සාරණ වේගය සහ අනෙකුත් ක්රියාවලි පරාමිතීන් සාධාරණ පාලනය කිරීම.
XXV.මුඛය පුළුල් කරන්න (සහ).
වලක් සහ I-හැඩය වැනි නිස්සාරණය කරන ලද පැතිකඩ නිෂ්පාදනවල පැති දෙක පිටතට නැඹුරු වී ඇති දෝෂය දැල්වීම ලෙස හැඳින්වේ, සහ ඇතුළතට නැඹුරු වන දෝෂය සමාන්තර විවරයක් ලෙස හැඳින්වේ.
ප්රසාරණයට ප්රධාන හේතු (ඒකාබද්ධ වීම)
1. අගලෙහි "කකුල්" දෙකේ (හෝ එක් "කකුලක්") හෝ ඊට සමාන අගල පැතිකඩවල හෝ I-හැඩැති පැතිකඩවල ලෝහ ප්රවාහ අනුපාතය අසමාන වේ;
2. වලක් පහළ තහඩුවේ දෙපස වැඩ කරන තීරයේ ප්රවාහ අනුපාතය අසමාන වේ;
3. නුසුදුසු දිගු සෘජු කිරීමේ යන්ත්රය;
4. නිෂ්පාදිතය අච්චු කුහරයෙන් පිටතට ගිය පසු, මාර්ගගත විසඳුම් ප්රතිකාරය අසමාන ලෙස සිසිල් කරනු ලැබේ.
වැළැක්වීමේ ක්රමය
1. නිස්සාරණ වේගය සහ නිස්සාරණ උෂ්ණත්වය දැඩි ලෙස පාලනය කරන්න;
2. සිසිලනය පිළිබඳ ඒකාකාරිත්වය සහතික කිරීම;
3. නිවැරදිව සැලසුම් කිරීම සහ අච්චු නිෂ්පාදනය කිරීම;
4. නිස්සාරණ උෂ්ණත්වය සහ වේගය දැඩි ලෙස පාලනය කරන්න, මෙවලම ස්ථාපනය කර නිවැරදිව මිය යන්න.
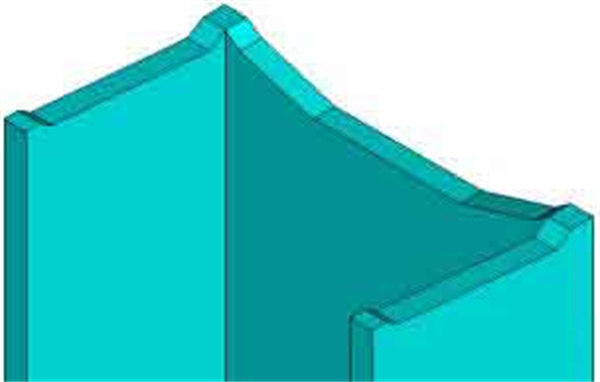
XXVI.සෘජු ලකුණු
නිස්සාරණය කරන ලද නිෂ්පාදනයේ ඉහළ රෝල් කෙළින් කරන විට නිපදවන හෙලික්සීය ඉරි කෙළින්ම ලකුණු ලෙස හැඳින්වේ, ඉහළ රෝලයෙන් කෙළින් කරන ලද ඕනෑම නිෂ්පාදනයක් සඳහා කෙළින් සලකුණු වළක්වා ගත නොහැක.
ලකුණු කෙළින් කිරීමට ප්රධාන හේතුව
1. සෘජු රෝලර් රෝලර් මතුපිට මත දාර ඇත;
2. නිෂ්පාදනයේ නැමීම ඉතා විශාලයි;
3. අධික පීඩනය;
4. සෘජු කිරීමේ රෝලරයේ කෝණය ඉතා විශාලය
5. නිෂ්පාදනයේ විශාල ovality ඇත.
වැළැක්වීමේ ක්රමය
හේතුව අනුව සකස් කිරීමට සුදුසු පියවර ගන්න.
XXVII.නැවතුම් ලකුණු, ක්ෂණික හැඟීම්, බයිට් ලකුණු
නිස්සාරණය අතරතුර නිස්සාරණය නවත්වා නිෂ්පාදනයේ මතුපිට ඉරි නිපදවීමට සහ නිස්සාරණ දිශාවට ලම්බකව, නැවතුම් සලකුණු ලෙස හැඳින්වේ;නිෂ්පාදනයේ මතුපිට රේඛා හෝ ඉරි ඉරි සහ නිස්සාරණයේදී නිස්සාරණ දිශාවට ලම්බකව, බයිට් ලකුණු හෝ ක්ෂණික හැඟීම් ලෙස හැඳින්වේ (සාමාන්යයෙන් "ව්යාජ වාහන නැවැත්වීමේ සලකුණු" ලෙස හැඳින්වේ)
නිස්සාරණය අතරතුර, වැඩ කරන පටියේ මතුපිටට ස්ථායීව ඇලී ඇති ඇමිණුම් ක්ෂණිකව වෙන් කර රටා සෑදීමට නිස්සාරණය කරන ලද නිෂ්පාදනයේ මතුපිටට ඇලී ඇත.නිස්සාරණය නැවැත්වූ විට දිස්වන වැඩ කරන පටියේ තිරස් තීරු වාහන නැවැත්වීමේ සලකුණු ලෙස හැඳින්වේ;නිස්සාරණ ක්රියාවලියේදී දිස්වන ඉරි ක්ෂණික හැඟීම් හෝ බයිට් සලකුණු ලෙස හැඳින්වේ, ඒවා නිස්සාරණයේදී ශබ්දයක් නිකුත් කරයි.
නැවතුම් ලකුණු, ක්ෂණික ලකුණු සහ කටගැස්ම සඳහා ප්රධාන හේතු
1. ඉන්ගෝට් වල අසමාන තාපන උෂ්ණත්වය හෝ නිස්සාරණ වේගය සහ පීඩනයෙහි හදිසි වෙනස් වීම;
2. අච්චුවේ ප්රධාන කොටස් දුර්වල ලෙස නිර්මාණය කර නිෂ්පාදනය කර ඇත, නැතහොත් එකලස් කිරීම අසමාන වන අතර හිඩැස් ඇත;
3. නිස්සාරණ දිශාවට ලම්බකව බාහිර බලයක් ඇත;
4. extruder සුමට ලෙස ක්රියාත්මක නොවන අතර, බඩගා යන සංසිද්ධියක් ඇත.
වැළැක්වීමේ ක්රමය
1. අධික උෂ්ණත්වය, මන්දගාමී වේගය සහ ඒකාකාර නිස්සාරණය, නිස්සාරණ බලය ස්ථාවරව පවතී;
2. නිෂ්පාදිතය මත ක්රියා කිරීමෙන් සිරස් නිස්සාරණ දිශාවෙහි බාහිර බලය වැළැක්වීම;
3. මෙවලම් සහ අච්චු සාධාරණ ලෙස නිර්මාණය කිරීම, අච්චු ද්රව්ය නිවැරදි තේරීම, ප්රමාණය ගැලපීම, ශක්තිය සහ දෘඪතාව.
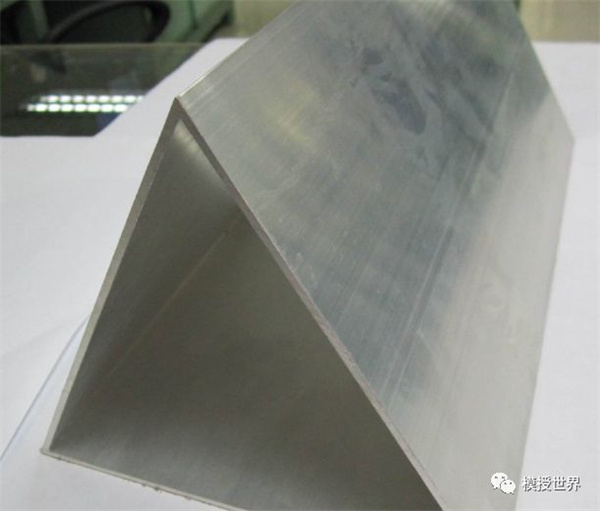
XXVIII.අභ්යන්තර පෘෂ්ඨයේ සීරීම්
නිස්සාරණ ක්රියාවලියේදී නිස්සාරණය කරන ලද නිෂ්පාදනයේ අභ්යන්තර පෘෂ්ඨයේ ඇති සීරීම් අභ්යන්තර මතුපිට සීරීම් ලෙස හැඳින්වේ.
අභ්යන්තර මතුපිට උල්ෙල්ඛයේ ප්රධාන හේතුව
1. නිස්සාරණ ඉඳිකටුවක් ලෝහ සමග සිරවී ඇත;
2. නිස්සාරණ ඉඳිකටුවෙහි උෂ්ණත්වය අඩුය;
3. නිස්සාරණ ඉඳිකටුවෙහි මතුපිට ගුණාත්මක භාවය දුර්වල වන අතර ගැටිති ඇත;
4. නිස්සාරණ උෂ්ණත්වය සහ වේගය හොඳින් පාලනය නොවේ;
5. නිස්සාරණ ලිහිසි තෙල්වල නුසුදුසු අනුපාතය;
වැළැක්වීමේ ක්රමය
1. නිස්සාරණ සිලින්ඩරයේ සහ නිස්සාරණ ඉඳිකටුවෙහි උෂ්ණත්වය වැඩි කිරීම, නිස්සාරණ උෂ්ණත්වය සහ නිස්සාරණ වේගය පාලනය කිරීම;
2. ලිහිසි තෙල් පෙරීම ශක්තිමත් කිරීම, අපද්රව්ය තෙල් නිතර පරීක්ෂා කිරීම හෝ ප්රතිස්ථාපනය කිරීම සහ තෙල් ඒකාකාරව හා සුදුසු ලෙස යොදන්න;
3. ලොම් මතුපිට පිරිසිදුව තබා ගන්න;
4. නුසුදුසු අච්චු සහ නිස්සාරණ ඉඳිකටු නියමිත වේලාවට ප්රතිස්ථාපනය කරන්න, සහ නිස්සාරණ අච්චු මතුපිට පිරිසිදුව හා සිනිඳුව තබා ගන්න.
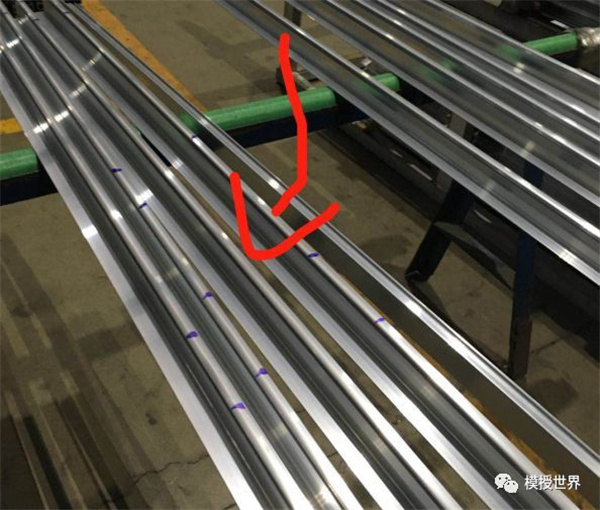
XXX.වෙනත් සාධක
වචනයෙන් කියනවා නම්, පුළුල් ප්රතිකාරයකින් පසු, ඉහත සඳහන් කළ ඇලුමිනියම් මිශ්ර ලෝහ නිස්සාරණ නිෂ්පාදනවල දෝෂ වර්ග 30 ක් effectively ලදායී ලෙස ඉවත් කර, උසස් තත්ත්වයේ, ඉහළ අස්වැන්නක්, දිගු ආයු කාලයක් සහ අලංකාර නිෂ්පාදන මතුපිටක්, වෙළඳ නාමයක් නිර්මාණය කර, ජීව ශක්තිය සහ සමෘද්ධිය ගෙන එයි. ව්යවසාය, සහ සැලකිය යුතු තාක්ෂණික සහ ආර්ථික ප්රතිලාභ ඇත.
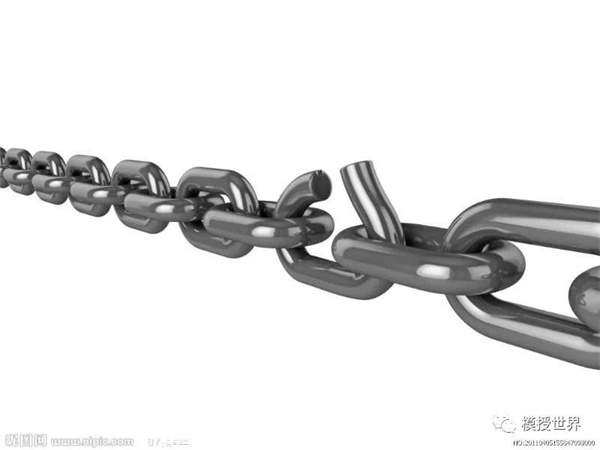
XXX.වෙනත් සාධක
වචනයෙන් කියනවා නම්, පුළුල් ප්රතිකාරයකින් පසු, ඉහත සඳහන් කළ ඇලුමිනියම් මිශ්ර ලෝහ නිස්සාරණ නිෂ්පාදනවල දෝෂ වර්ග 30 ක් effectively ලදායී ලෙස ඉවත් කර, උසස් තත්ත්වයේ, ඉහළ අස්වැන්නක්, දිගු ආයු කාලයක් සහ අලංකාර නිෂ්පාදන මතුපිටක්, වෙළඳ නාමයක් නිර්මාණය කර, ජීව ශක්තිය සහ සමෘද්ධිය ගෙන එයි. ව්යවසාය, සහ සැලකිය යුතු තාක්ෂණික සහ ආර්ථික ප්රතිලාභ ඇත.
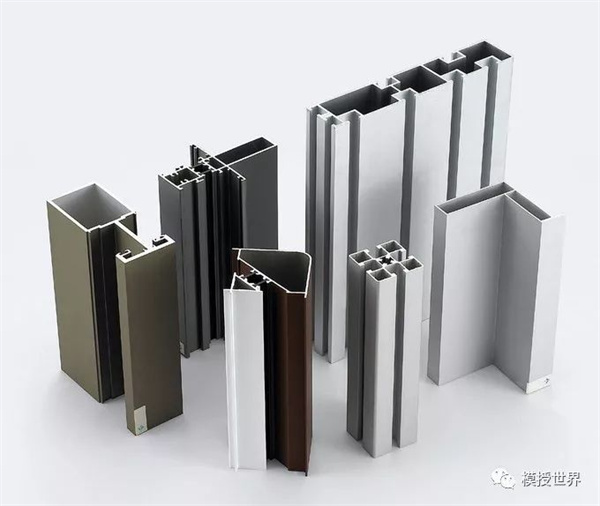
පසු කාලය: අගෝස්තු-14-2022